Enhancing Accuracy in Multi Jet Fusion Quotes
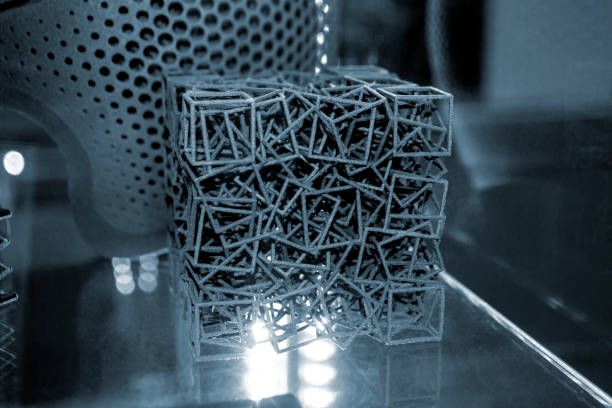
Multi Jet Fusion (MJF) is a game-changing 3D printing technology that offers unparalleled speed, precision, and cost-effectiveness for producing complex parts. As more businesses embrace this innovative manufacturing method, understanding the quoting process becomes crucial for making informed decisions and optimizing production workflows.
Accurate quoting is essential for manufacturers, engineers, and product designers who seek to leverage the benefits of MJF technology while managing costs and meeting project timelines. By familiarizing themselves with the factors that influence MJF pricing, professionals can make well-informed choices when selecting service providers and planning their manufacturing strategies.
In this article, we will dive into the intricacies of MJF quoting, exploring the key elements that impact pricing and sharing best practices for enhancing accuracy in the quoting process. Whether you are a seasoned professional or new to the world of additive manufacturing, understanding the nuances of MJF quoting can help you unlock the full potential of this cutting-edge technology and drive success in your projects.
What is Multi Jet Fusion Quoting?
Multi Jet Fusion quoting is the process of estimating the costs associated with producing parts using HP's groundbreaking 3D printing technology. This involves a comprehensive evaluation of various factors that influence the final price, such as material selection, design complexity, production volume, and turnaround time. By carefully considering these elements, manufacturers and service providers can generate accurate quotes that align with client expectations and project requirements.
The importance of precision in MJF quoting cannot be overstated. Accurate quotes not only help to maintain profitability for the service provider but also ensure that clients have a clear understanding of the costs involved in bringing their designs to life. Inaccurate quotes can lead to misaligned expectations, project delays, and potential financial losses for both parties.
To streamline the quoting process and enhance accuracy, many service providers are turning to advanced technology and automation. Platforms like Phasio offer instant quoting capabilities for MJF parts, leveraging powerful algorithms and extensive databases to provide fast and reliable price estimates. By incorporating these tools into their workflow, manufacturers can significantly reduce the time and effort required for quoting while maintaining a high level of precision.
Embracing the power of advanced quoting technology is essential for manufacturers seeking to thrive in the fast-paced world of Multi Jet Fusion production. By leveraging innovative platforms and data-driven insights, we can elevate the accuracy and efficiency of our quoting processes, ultimately delivering unparalleled value to our clients. Witness firsthand how our cutting-edge solutions can revolutionize your manufacturing workflow.
Key Factors in MJF Quoting
When generating a quote for an MJF project, several critical factors come into play:
- Material Costs: The choice of material, such as Nylon 12 or Polypropylene, directly impacts the overall cost of the project. Each material has its own unique properties and price point, which must be carefully considered during the quoting process.
- Design Complexity: The intricacy of the part design can significantly influence the production time and cost. Complex geometries, fine details, and large overhangs may require additional processing steps or support structures, which can add to the final price.
- Production Volume: The number of parts being produced plays a crucial role in determining the cost per unit. Higher volumes often result in lower per-unit costs due to economies of scale and more efficient utilization of the MJF equipment.
- Turnaround Time: The urgency of the project and the required delivery date can impact the quoting process. Rush orders or expedited production may incur additional fees to accommodate the accelerated timeline.
By carefully analyzing these factors and leveraging advanced quoting tools, manufacturers can provide accurate and competitive quotes for MJF projects. This not only helps to build trust with clients but also ensures that the production process runs smoothly and efficiently, ultimately leading to successful outcomes for all parties involved.
How to Enhance Accuracy in Multi Jet Fusion Quotes
Improving precision in Multi Jet Fusion (MJF) quotes involves a careful blend of detailed evaluation and innovative technology. Accurate cost assessments form the backbone of effective project management, ensuring that both client requirements and operational margins are fully considered. Each aspect of the quoting process must reflect real production scenarios to provide credible estimates.
Leveraging Advanced Tools and Automation
Integrating advanced tools and automation into the quoting process transforms how estimates are generated. Such systems can efficiently evaluate key variables, including material selection and production timelines, delivering precise estimates quickly. This approach minimizes manual errors and accelerates response times, giving manufacturers a competitive edge.
- Sophisticated Software Solutions: Employing sophisticated software capable of analyzing intricate cost components ensures reliable quotes. These solutions take into account detailed project specifications, offering a comprehensive pricing model.
- CAD Software Integration: Linking quoting systems with CAD software enhances the evaluation of design intricacies. This connection allows for comprehensive assessments of potential manufacturing challenges, ensuring that quotes are both realistic and accurate.
Embracing Continuous Improvement
A commitment to ongoing refinement is crucial for enhancing the accuracy of MJF quotes over time. By leveraging data from completed projects, manufacturers can refine their processes and improve future estimates.
- Data-Driven Adjustments: Systematic reviews of project data help identify cost prediction discrepancies, enabling process adjustments that enhance future quoting accuracy.
- Client Engagement: Actively seeking client input on the quoting experience reveals insights for refinement. This feedback helps adjust processes to better meet client needs, strengthening partnerships.
By utilizing cutting-edge tools and fostering a culture of continuous improvement, manufacturers can ensure their MJF quotes are as precise and efficient as possible. This not only builds client confidence but also establishes the manufacturer as a leader in the additive manufacturing sector.
Step 1: Analyzing Material Costs
Analyzing material costs is a pivotal step in enhancing the accuracy of Multi Jet Fusion (MJF) quotes. Selecting the appropriate materials involves understanding their distinct benefits and financial implications. This understanding helps manufacturers align material choices with project requirements and budget constraints.
Evaluating Material Options
Selecting the right material involves more than just cost considerations. Each material offers unique properties that can affect the final product's performance and suitability for specific applications.
- Nylon 12: Renowned for its robustness, Nylon 12 offers outstanding resilience and dimensional stability. Its suitability for detailed features and smooth finishes makes it a preferred option for both functional prototypes and production parts.
- Polypropylene: Known for its toughness and resistance to chemicals, Polypropylene is ideal for parts that need to endure challenging environments. Its cost-effectiveness makes it an appealing choice for projects where economic factors are critical.
Aligning Material Properties with Project Needs
The success of a project depends significantly on how well the selected material meets the technical requirements. Manufacturers must consider factors such as part functionality, environmental exposure, and mechanical demands when analyzing material costs.
- Technical Compatibility: Ensuring that the material's properties align with the intended use of the part is essential. For example, parts requiring flexibility and impact resistance might benefit from the unique characteristics of the selected material.
- Cost-Benefit Analysis: Balancing the cost of materials with their performance benefits is crucial. Conducting a thorough evaluation allows manufacturers to make strategic decisions that optimize both budget and product functionality.
Through a comprehensive evaluation of material options and their associated costs, manufacturers can provide more accurate and competitive MJF quotes, enhancing client satisfaction and project success.
Step 2: Assessing Design Complexity
The intricacies inherent in a design significantly influence the Multi Jet Fusion (MJF) quoting process. Conducting a detailed evaluation of design specifications allows manufacturers to pinpoint areas that might pose challenges during production. This involves examining features such as intricate patterns, delicate geometries, and areas where precision is paramount, which could impact the ease and cost of manufacturing.
Utilizing Predictive Tools for Evaluation
To refine the quoting process, manufacturers increasingly adopt predictive tools that evaluate design files for potential production hurdles. These advanced systems offer valuable insights into a design's feasibility, highlighting areas that might affect manufacturing outcomes. Such technology integration ensures that quotes encompass all relevant design aspects, reducing the likelihood of unexpected issues.
- Predictive Design Analysis: Employing predictive analysis tools offers a comprehensive review of the design, identifying characteristics that may complicate MJF production. This approach aids in optimizing the design and ensures quotes are based on informed projections.
- Rapid Quoting Systems: State-of-the-art quoting solutions employ predictive evaluations to generate swift, precise estimates. These systems consider the design's complexity and its implications for the manufacturing workflow, delivering accurate cost assessments efficiently.
Through rigorous assessment of design intricacies and the application of predictive tools, manufacturers can enhance the accuracy of their MJF quotes, aligning them with both client expectations and production realities.
Step 3: Estimating Production Volume and Speed
Estimating production volume and speed in the Multi Jet Fusion (MJF) quoting process involves a precise understanding of how these factors influence manufacturing efficiency and cost. This estimation is crucial for developing quotes that accurately reflect the realities of production while optimizing resource allocation. By strategically considering these elements, manufacturers can ensure cost-effective operations and enhance client satisfaction.
Batch Size Considerations
Determining the appropriate batch size is pivotal in maximizing production efficiency. Larger batches often lead to cost reductions per unit by spreading fixed expenses over more items, which can improve overall project profitability.
- Maximizing Throughput: Producing larger quantities in a single run can enhance throughput, as this approach makes better use of the machine's capacity and reduces the frequency of setup changes. This strategy helps maintain a steady production flow, minimizing downtime and enhancing cost efficiency.
- Optimized Resource Allocation: Thoughtful batch size planning ensures that material and labor resources are utilized effectively, preventing bottlenecks and waste. By aligning batch sizes with operational capabilities, manufacturers can streamline production processes for better outcomes.
Harnessing MJF's Speed
The rapid production capabilities of MJF technology provide a significant advantage in meeting tight deadlines and accommodating fluctuating demand. By fully leveraging these capabilities, manufacturers can improve their responsiveness to market needs and client expectations.
- Expedited Production Cycles: The swift layer-by-layer construction inherent to MJF allows for shorter production cycles, enabling manufacturers to deliver products more quickly. This capability is particularly beneficial for projects with time constraints, giving manufacturers a competitive edge.
- Dynamic Scheduling Flexibility: MJF's high-speed production facilitates adaptable scheduling, allowing manufacturers to adjust timelines as needed without compromising quality. This flexibility supports a wide range of project requirements, making MJF a versatile choice for diverse manufacturing needs.
By accurately assessing production volume and efficiently utilizing the speed of MJF technology, manufacturers can offer precise and competitive quotes. This approach not only enhances client relationships but also positions manufacturers as leaders in the forward-thinking realm of additive manufacturing.
Step 4: Incorporating Labor and Overhead Costs
Incorporating labor and overhead costs into Multi Jet Fusion (MJF) quotes provides a comprehensive understanding of the total project expenses. These costs reflect the operational nuances of running a 3D printing facility, encompassing both direct and indirect expenses. By integrating these aspects into the pricing structure, manufacturers can offer quotes that truly represent the investment required for production.
Evaluating Labor Contributions
Labor costs include the expertise of personnel who ensure the smooth operation of MJF technology. This entails understanding the time invested in machine management, quality assurance, and part handling, all essential for maintaining production efficiency.
- Expert Management: Skilled operators play an indispensable role in maintaining MJF systems. Their ability to manage machine parameters and address issues promptly ensures consistent production quality.
- Comprehensive Time Assessment: Analyzing the hours dedicated to all production-related activities, including equipment monitoring and part inspection, offers a transparent view of labor requirements.
Calculating Overhead Expenses
Overhead costs, which include utilities, maintenance, and other facility-related expenses, are crucial in supporting the infrastructure required for effective MJF operations. These costs ensure that the facility remains capable of sustaining high-quality outputs.
- Operational Expenditures: Regular expenses such as energy consumption for printers and environmental controls are vital considerations. Proper allocation of these costs guarantees a stable production environment.
- Long-term Asset Management: Recognizing the depreciation of MJF equipment over time allows for strategic resource allocation, ensuring a balance between capital investment and production capabilities.
By accurately incorporating labor and overhead expenses into MJF quotes, manufacturers can provide detailed and reliable estimates that reflect the true cost of production. This approach enhances client confidence and aligns project pricing with the operational realities of modern manufacturing.
Step 5: Utilizing Technology for Accurate Quoting
Integrating cutting-edge technology into the quoting process revolutionizes how estimates are generated in Multi Jet Fusion (MJF) projects. By adopting innovative quoting platforms, manufacturers can provide rapid, detailed cost evaluations that cater to complex production requirements. These systems seamlessly incorporate into existing operations, offering a comprehensive framework that considers various factors—ranging from design intricacies to material properties—with exceptional precision.
Streamlined Processes with Innovative Platforms
Incorporating advanced quoting platforms eliminates the inefficiencies of traditional methods, ensuring reliable and timely cost assessments. These platforms utilize sophisticated algorithms to assess key variables, delivering insightful cost breakdowns that align with actual production scenarios.
- Sophisticated Algorithm Utilization: Advanced platforms leverage powerful algorithms to conduct swift assessments, evaluating multiple scenarios to present competitive pricing. This approach not only expedites the quoting process but also enhances the reliability of the projections made.
- Insightful Data Analytics: Through data analytics, these platforms provide actionable insights, enabling manufacturers to dynamically adjust parameters and optimize pricing strategies. This adaptability ensures that quotes remain market-relevant and informed by current trends.
Elevating Client Experience
The accuracy and efficiency provided by these technological advancements significantly bolster client satisfaction. Clients receive transparent, comprehensive quotes that facilitate informed decision-making and build confidence in the service provided.
- Responsive Adjustments: Equipped with real-time data capabilities, these platforms can swiftly integrate changes, ensuring quotes are consistently up-to-date with the latest project details. This agility fosters trust and enhances client relationships.
- Reputation for Reliability: Delivering consistently precise quotes establishes a reputation for dependability, setting manufacturers apart in a competitive landscape. This reliability not only meets client expectations but also reduces the risk of unexpected costs, strengthening long-term business partnerships.
Utilizing advanced quoting technology is essential in the realm of MJF, streamlining processes and ensuring the highest standards of accuracy in cost estimation. Through innovative platforms and real-time data integration, manufacturers can confidently navigate the demands of modern production environments.
Embracing the power of advanced quoting technology is essential for manufacturers seeking to thrive in the fast-paced world of Multi Jet Fusion production. By leveraging innovative platforms and data-driven insights, we can elevate the accuracy and efficiency of our quoting processes, ultimately delivering unparalleled value to our clients. If you're ready to transform your MJF quoting experience, schedule a demo or try the platform to witness firsthand how our cutting-edge solutions can revolutionize your manufacturing workflow.